Spring Into Action: Why Warm Weather is the Perfect Time for Fitness Equipment Repairs in St. Louis
As St. Louis emerges from winter and members return to fitness routines with renewed enthusiasm, your equipment faces increased demands just as you're heading into the busy summer season. That treadmill belt that's been showing slight wear? The strength machine with the occasional cable hitch? The elliptical making that barely noticeable sound? These minor issues can quickly evolve into major problems precisely when your facility needs to be operating at peak performance.
Smart facility operators across the St. Louis region recognize that spring and early summer represent the ideal window for proactive equipment repairs—addressing small issues before they become disruptive breakdowns during your busiest months.
The St. Louis Seasonal Fitness Cycle
Anyone who's operated a fitness facility in St. Louis understands our region's distinct seasonal patterns. As the humidity drops and temperatures become more inviting, indoor workout spaces experience the dual impact of returning seasonal members and regular members increasing their training frequency.
From Clayton to South County, from St. Charles to Metro East, this pattern repeats itself. The moderate spring weather creates perfect conditions for fitness enthusiasm before the intense summer heat drives even more members indoors to air-conditioned facilities. This predictable cycle means that equipment that performed adequately during lower-volume winter months suddenly reveals its vulnerabilities under increased usage.
For facility operators, this creates a critical opportunity. The window between winter's slower pace and summer's peak traffic provides the perfect timing for systematic equipment assessment and repair. Addressing issues during this transitional period minimizes disruption while maximizing equipment availability when your facility needs it most.
Beyond the Emergency Call: The Case for Preventative Repairs
Most St. Louis fitness facilities operate in a reactive maintenance mode—waiting until equipment fails before calling for repairs. While understandable from a short-term budgeting perspective, this approach ultimately costs more in both financial terms and member satisfaction.
Consider what happens when a popular piece of equipment fails during peak hours on a busy summer day. Beyond the immediate repair costs, you face member frustration, potential safety concerns, and the operational challenge of managing traffic around unavailable equipment. For specialty pieces with limited alternatives in your facility, these failures can significantly impact specific member segments.
Preventative repair approaches identify and address emerging issues before they cause equipment failure. The slightly worn drive belt, the bearing that's beginning to show play, or the frame bolt that's gradually loosening—these minor issues can be addressed quickly during a planned maintenance window rather than requiring emergency service and extended downtime during busy periods.
The Repair Roaster: What Needs Attention Now
As St. Louis moves into the warmer months, specific equipment components face increased stress. Our region's notorious humidity affects electronic components, while higher usage impacts mechanical systems. Experienced facility operators focus on these critical areas during spring maintenance:
Cardio Equipment Drive Systems
Treadmill belts and decks face extraordinary wear as usage increases. The transition to spring provides the perfect opportunity to assess belt condition, deck lubrication, and drive motor performance before summer demand peaks. Replacing a moderately worn belt in April prevents a complete failure in July when replacement would cause maximum disruption.
Cable Systems and Pulleys
The increased usage of strength equipment during spring and summer means greater stress on cable systems. Fraying cables, worn pulleys, and bearing issues identified and addressed early prevent mid-workout failures that can create both member disappointment and potential safety issues.
Electronic Consoles and Connections
St. Louis's spring humidity followed by intense air conditioning creates challenging conditions for electronic components. Preventative cleaning, connection tightening, and software updates prepare these systems for reliable summer performance.
Upholstery and Member Contact Points
Higher member traffic means increased wear on upholstery, grips, and other contact surfaces. Addressing tears, splits, and wear before they worsen protects both aesthetics and hygiene during the sweaty summer months.
The Hidden Benefits of Spring Repairs
Beyond simply avoiding breakdowns, strategic spring equipment repairs deliver additional benefits that many facility operators overlook:
Extended Equipment Lifespan
Regular interventions significantly extend the useful life of fitness equipment. In an industry where capital costs represent a major budget item, adding years to your equipment through proper maintenance delivers substantial financial benefits.
Enhanced Member Experience
Equipment that functions flawlessly creates a premium experience that members notice—even if they don't specifically attribute it to your maintenance protocols. The smooth treadmill belt, the silent elliptical drive, and the fluid cable motion all contribute to workout satisfaction.
Optimized Summer Staffing
When your equipment runs reliably, your staff spends less time managing member complaints, creating "out of order" signs, and rearranging workout spaces to accommodate non-functional equipment. This operational efficiency becomes particularly valuable during busy summer months.
Energy Efficiency
Well-maintained equipment operates more efficiently, reducing power consumption during the high-cost summer cooling season. From properly lubricated treadmill decks to optimized electronic systems, preventative repairs often deliver energy savings that accumulate over time.
The EcoFit Approach: Beyond Basic Repairs
While any service provider can replace obviously broken parts, EcoFit's St. Louis repair teams bring a more comprehensive approach to fitness equipment maintenance. Our technicians don't just fix what's broken—they identify underlying issues and emerging problems before they affect performance.
This diagnostic approach begins with systematic evaluation. Rather than focusing exclusively on the reported problem, our technicians assess overall equipment condition, identifying wear patterns and potential failure points that might not yet be apparent during normal operation.
For St. Louis facilities, this local expertise provides particular value. Our repair teams understand how the region's specific conditions—from humidity fluctuations to power quality issues in different areas—affect equipment performance. This specialized knowledge allows for targeted interventions that address not just symptoms but underlying causes.
Component Quality: The Repair Decision That Matters
When repairs are necessary, component selection significantly impacts long-term outcomes. Many service providers use generic replacement parts that deliver initial functionality but fail prematurely under regular use.
EcoFit's repair philosophy prioritizes appropriate component selection—using OEM (Original Equipment Manufacturer) parts when necessary for critical systems while offering cost-effective alternatives for less demanding applications. This balanced approach ensures reliable repairs without unnecessary expense.
For St. Louis facilities preparing for the summer season, this component quality becomes particularly important. Replacement parts that might perform adequately under light usage often fail quickly when subjected to the intense demands of peak summer traffic. Our repair recommendations consider not just current conditions but anticipated usage patterns throughout the season.
Minimizing Disruption: Repair Logistics That Work
Even necessary repairs can create operational challenges if poorly timed or inefficiently executed. EcoFit's St. Louis repair teams work with your facility to develop maintenance schedules that minimize member impact while maximizing equipment availability.
This logistical expertise includes:
- Early morning or late evening repair windows for minimal disruption
- Coordinated repair scheduling that maintains alternatives for members
- Expedited approaches for popular equipment with limited redundancy
- Transparent communication to help manage member expectations
For seasonal facilities like pool clubs and outdoor training centers across the St. Louis region, our repair teams can provide comprehensive equipment revival services before your peak season begins, ensuring that all systems are functioning optimally from opening day.
From Repairs to Reliability: The Maintenance Partnership
The most successful fitness facilities in St. Louis approach equipment repairs not as isolated events but as components of a comprehensive maintenance strategy. This perspective shifts the focus from emergency response to planned reliability.
EcoFit supports this approach through preventative maintenance programs tailored to each facility's specific equipment mix, usage patterns, and budget constraints. For many clients, these programs begin with spring readiness service that addresses accumulated winter issues while preparing for increased summer demands.
These partnerships provide predictable costs, reduced emergency service needs, and extended equipment lifespans—all contributing to improved operational performance during critical high-volume periods.
Your Spring Repair Checklist
As you prepare your St. Louis facility for the busy season ahead, consider these key areas for spring repair assessment:
Cardio Equipment
- Treadmill belt and deck condition
- Drive system tension and alignment
- Console functionality and connectedness
- Safety features and emergency stops
Strength Equipment
- Cable integrity throughout full range of motion
- Pulley alignment and bearing condition
- Frame connection tightness and stability
- Upholstery condition, especially at high-wear points
Functional Training Systems
- Anchor point security and stability
- Adjustable component function
- Surface conditions for plyometric elements
- Stability for freestanding structures
Addressing these critical areas now prevents disruptions during your facility's busiest months while ensuring that members experience consistent quality throughout the summer season.
Start Your Summer Strong
Don't wait for the heat and humidity of a St. Louis summer to reveal equipment weaknesses. EcoFit's repair teams are ready to help your facility address existing issues, prevent emerging problems, and optimize your equipment for the demanding months ahead.
With specialized knowledge of fitness facilities throughout the St. Louis region, from downtown boutique studios to suburban multipurpose centers, our repair specialists deliver solutions tailored to your specific needs. Contact us today to schedule your spring equipment assessment and enter the busy season with confidence in your facility's operational readiness.
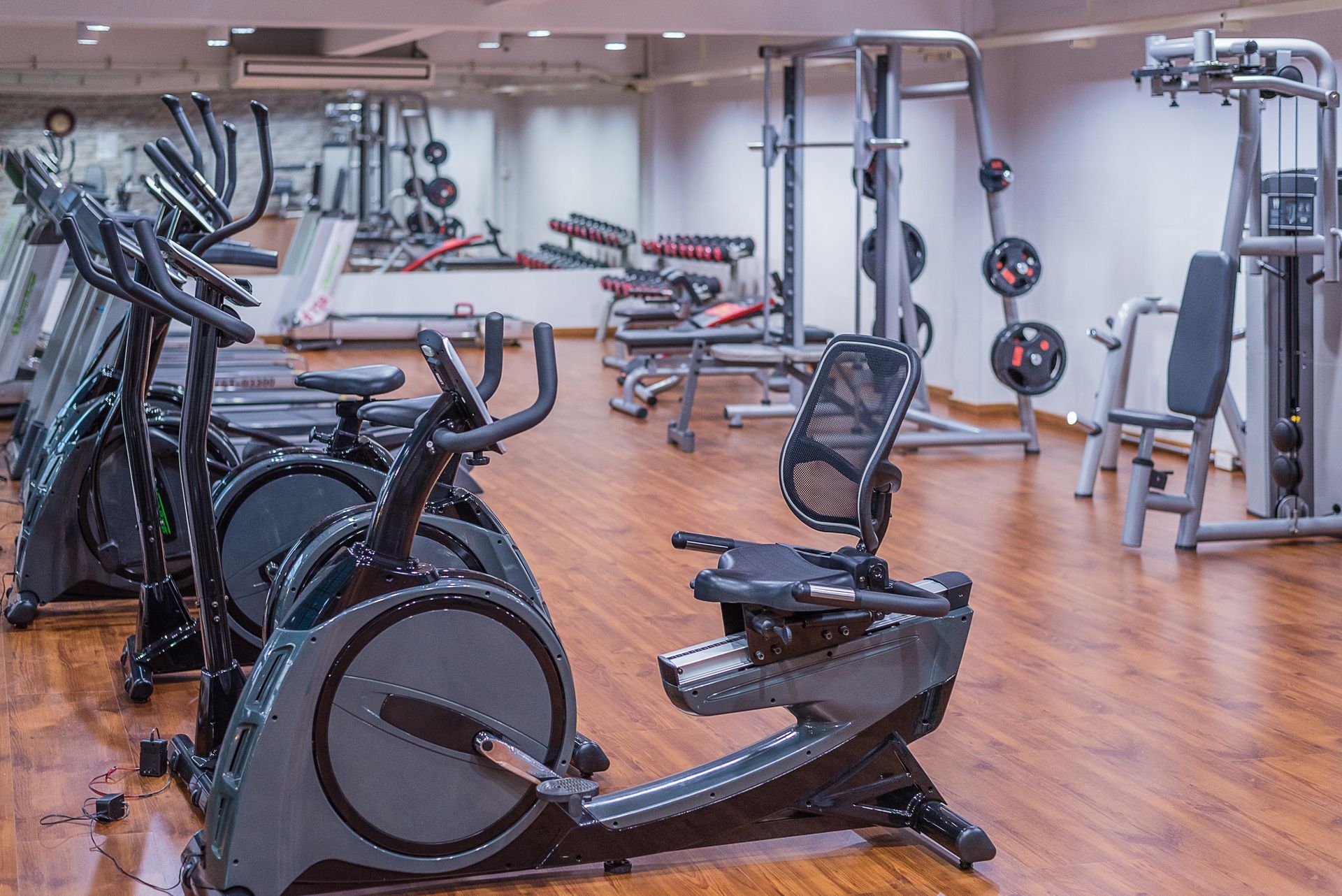
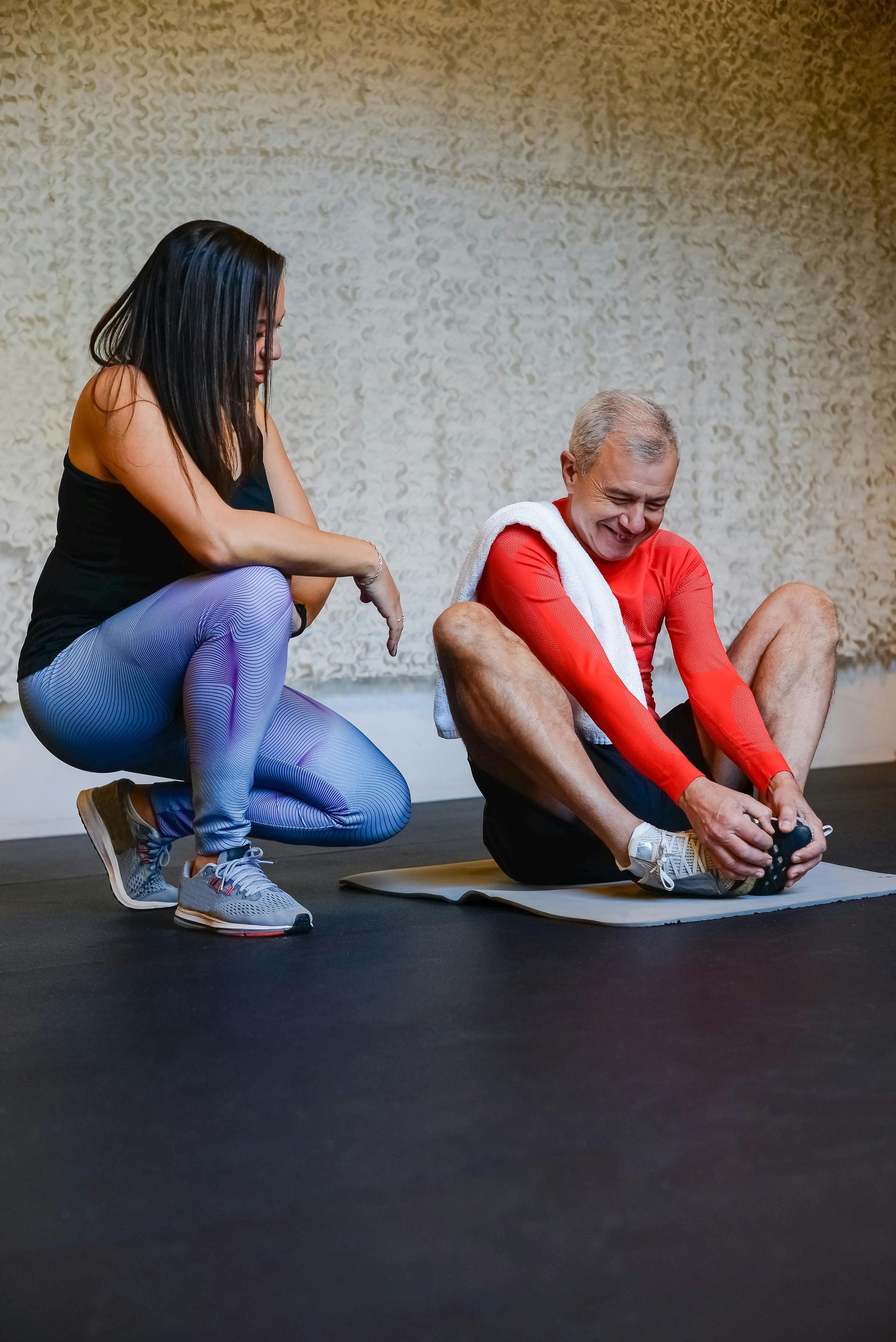
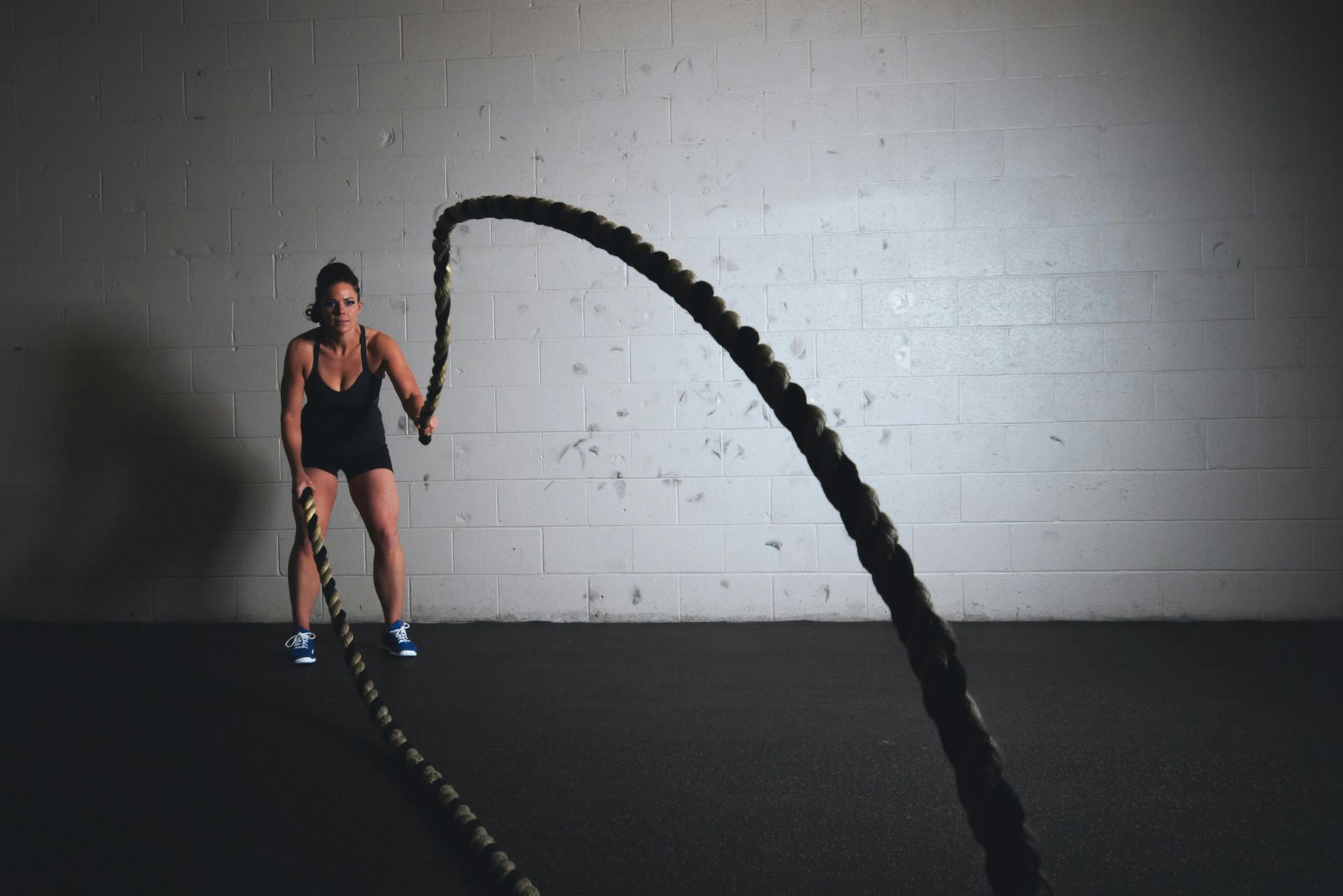